Dietz and Watson
Food & Beverage
Philadelphia, PA, USA
Philadelphia, PA || Baltimore, MD || Corfu, NY
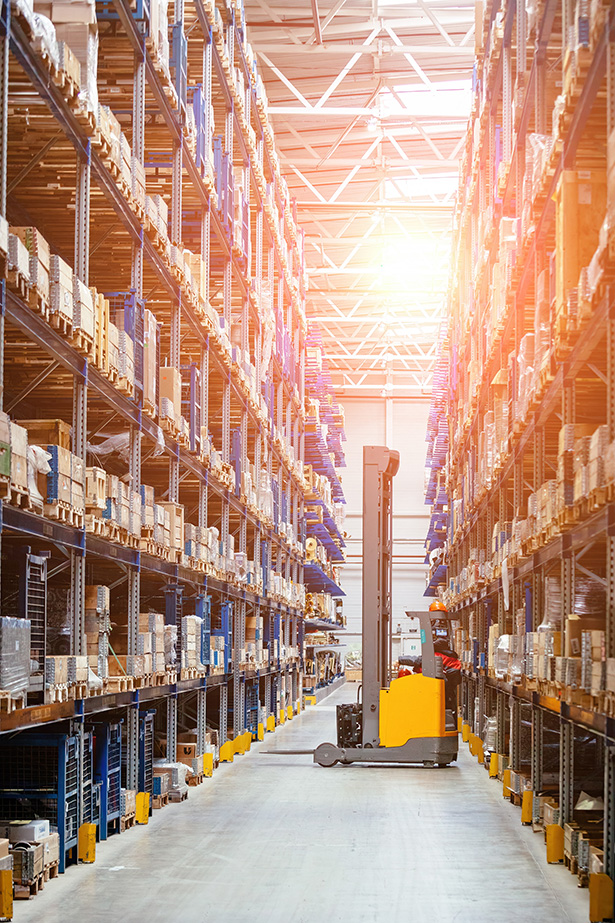
Overview
Perfection and originality has been the mission for Dietz and Watson since its origin in 1939. Today, at Dietz and Watson, the third generation continues Founder Gottlieb Dietz’s dedication and commitment to preparing and distributing premium deli meats and artisan cheeses. It is in this relentless pursuit of excellence that they realized the need for a world class technology solution that could meet their growing distribution needs.
The distribution center is approximately 300,000 square feet with several different temperature controlled areas ranging from 28 to 34 degrees all the way down to freezers kept at minus 10. Having many product lines and variables to manage, Dietz & Watson wanted a strategic implementation plan that had the lowest impact on their daily operations while continuing to provide a high level of service to their customers.
The key decision drivers were cost of ownership, strength of the vendor, ability to compliment future growth with operational efficiencies and robust ancillary functionality. While Dietz & Watson was initially only interested in the WMS, they wanted a solution that positions them to easily integrate complementing functions in the future. The selection was narrowed down from 14 companies and finally Softeon was selected for their state of the art architecture, robust functionality, and customer service/ support reputation. Also significant was Softeon’s suite of robust solutions that included Order Management, Labor Management, Transportation, and Slotting, which could be easily integrated at a later time.
Dietz & Watson partnered with Black Bear Distribution, their third party logistics provider in Delanco, New Jersey, to install Softeon’s supply chain execution (SCE) solutions. Their provider was also very impressed with Softeon’s solution offering significant core (out-of-the-box) features that normally require costly enhancements to solutions from other leading vendors.
Business
Challenges
Dietz and Watson distribution centers traditionally maintained error-prone paper reports and manually put away and retrieved items within the warehouse.
As a result, they were physically out of space, and had zero visibility across the company for associates to communicate needs from inventory to customer service questions. DSD (Direct to Store Distribution) shipments, were very time consuming and labor intensive, and needed to be managed more quickly and efficiently.
Softeon Solution
Softeon’s advanced solution is 100% serialized down to the case, offering a complete tracking and trace functionality. RF technology is used for all shipping transactions and each order is tracked in real-time.
The system has the ability to capture catch weights, by product, to ensure order and billing accuracy. For customers that have special requirements, such as special “sale by dates,” the system handles those requirements automatically. The system fully supports any recall functionality that may be needed along with QA holds and incubation time holds.