Warehouse Management Systems (WMS) and software continue to see high rates of adoption, driven by a number of factors, including the growth of ecommerce and efulfillment processes, wider adoption of robots and other forms of automation in the distribution center, and interest in moving to Cloud-based WMS solutions. Of course, WMS integration is a key aspect in the successful deployment of
Warehouse Management software, but that’s not saying it strongly enough. Turning-on a new WMS is dependent on warehouse management system integration to a variety of external systems. And indeed, poorly executed WMS integrations have delayed or even scuttled WMS deployments. Thankfully, this is less common today than in the past.
There are several main types of systems requiring WMS integration. Those are:
WMS integration to ERP/Enterprise Systems
A WMS must almost always integrate with various ERP’s and other enterprise systems, whether that is SAP, Oracle, Infor, JD Edwards or numerous others, including home grown systems.
At a high level, integration from these enterprise systems to the WMS involves: master data (such as the item and/or customer master files), expected Purchase Order receipts, and customer orders that must be picked, packed and shipped.
From the WMS to enterprise systems, the data can include: changes to master data, such as carton dimensions for new products; receipts by PO; inventory changes and adjustments, such as altered due to picking and shipping orders or from cycle count adjustments; order status (if desired to make available for customers); and shipping confirmations, which can trigger the invoicing progress. Other WMS integrations are also common – one example being worker performance data to support incentive pay programs.
WMS integration to Customer Systems
In some cases, there is a need to directly integrate with customer systems. This is especially true in the third-party logistics sector to receive expected receipt information or customer order data. This is similar to integration to enterprise systems, but just a little different as the custom systems are not directly controlled by the company using the WMS.
WMS integration to Material Handling Systems
This is a broad category and includes everything from traditional conveyor sortation systems to new age autonomous mobile robots and much more in between, each with its own data, protocol, and nuances. We will note one key point, which is that picking sub-systems (mobile robots or pick-to-light systems, etc.) generally come with their own software that must be integrated with the WMS. An alternative approach from Softeon is to integrate directly with these sub-systems at the API level, eliminating the need for the other software. This approach has many cost and operational advantages versus throwing orders “over the wall” to the third-party sub-system software for execution, and receiving confirmations back on the work performed.
WMS integration to Other Supply Chain Systems
There is sometimes the need for the WMS to integrate with other existing or planned supply chain systems. Commonly, this includes Transportation Management Systems (TMS), Parcel Management software, label printing software, and occasionally CRM systems as well as others. Again, this scenario changes with Softeon, providing its own Parcel Shipping, TMS and label printing capabilities, which can be deployed pre-integrated with the WMS, though integration with third party systems in these and other areas is always an option.
WMS integration to Other Hardware and Peripherals
The WMS may need to integrate with other hardware and peripheral systems, including weigh scales, dimensioning equipment such as the Cubicscan, label print and apply (PANDA) systems, Voice systems and more. These are generally fairly straight forward, and again, Softeon offers its own solutions that can be pre-integrated with our WMS, such as with Softeon Voice.
Make Sense of WMS, WCS, and WES.
Understand the differences and how they work together to optimize your operations.
WMS Integration – the Key to Success
Through about 500 system deployments, Softeon has learned quite a bit about WMS integration. We see the following as important keys to success:
Look for Flexibility in Integrations: Some WMS vendors are very rigid in their approaches to integration, which can lead to problems and inflated costs. Look for a WMS vendor that will send and accept the data in any format you choose (xml, web hooks, REST APIs, flat files, EDI, etc.). This typically will significantly reduce a company’s internal effort on WMS integrations.
Evaluate a Potential WMS Vendor’s Tool Set: What tools does a potential WMS vendor bring to the integration effort? A robust tool set can reduce costs and risk. Softeon’s Enterprise Integration Workbench (EIW) includes an integration configurator and mapping tool; an integration simulator; and a real-time Interface Monitor, which continuously tracks all communications between the Softeon WMS and both enterprise and material handling systems, sends alerts if there any integration issues, allows simple message issues to be fixed on the spot; and much more.
The simulator is another powerful tool in the EIW, allowing messaging performance to be well-tested long before go-live. This is especially valuable for material handling system integrations.
A graphic of Softeon’s approach to enterprise system integrations using its Enterprise Integration Workbench (EIW) is provided below:
Softeon EIW: ERP/Enterprise Systems to Softeon WMS Platform
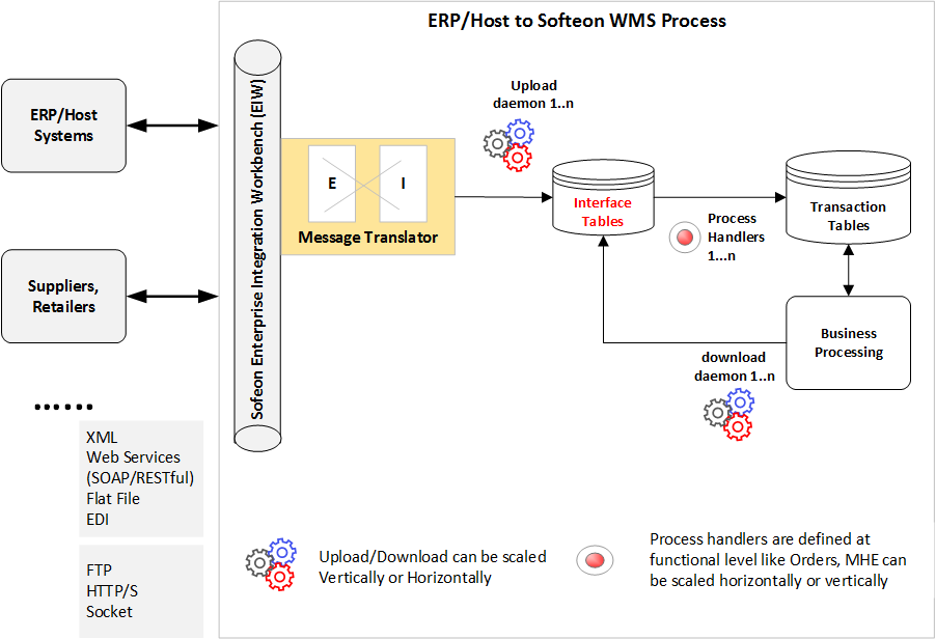
Get WMS Integrations Done Early in the Project: No one ever has enough resources, but not having the integrations completed at the time of system testing can really limit the level of testing that can be fully performed, thus adding to go-live risk.
Understand What is Happening with Material Handling System Integrations: WMS integrations with material handling systems can be a bit of a “black box” that adopting companies sometimes pay insufficient attention to, leaving the WMS and equipment vendors to sort it out. It is in your best interest to stay involved in these discussions.
Look for Plug-and-Play Materials Handling System Integration: With the rapidly growing adoption of DC automation of all types, look for a WMS platform that can add new types of equipment in an almost plug-and-play fashion. This includes the direct API-level integration that Softeon often uses for WMS integration with picking sub-systems as discussed above, with a unique approach to integration with mobile robots that allows robots of different types and manufacturers to be simultaneously operating and optimized on the Softeon platform.
This plug-and-play approach is also key to rapidly testing and deploying new technologies over time.
WMS integration – it really is the foundation of WMS project success. Look for a Warehouse Management System provider that has a highly flexible approach and a tool set and platform that minimizes the costs and risks of integrating WMS with ERP/enterprise, material handling systems and other applications and equipment.