A quality Warehouse Management System and Software implementation is obviously key to a successful outcome. In fact, the effects of a poor implementation can often linger for many months.
WMS implementations are specifically challenging compared to other supply chain software implementations for several reasons.
- A WMS must synchronize the physical world of buildings, inventory, equipment and people with the logical world of the warehouse software. This is not an easy task.
- Many distribution centers have complex operations, with multiple processing areas and product flows. There is often a myriad of things to get right.
- There are often dependencies in product flows, meaning that problems in one area can lead to upstream or downstream issues in other areas. For example, falling behind in order picking can lead to “stale” associates in packing without enough work to do.
- Finally, there is growing adoption of material handling system automation in many DCs, which requires tight integration between the WMS and the equipment control systems, plus orchestration of product flows into and out of the automation.
WMS implementation Project Roles and Responsibilities
One of the key early steps in a WMS implementation project is determining what internal resources are required and what roles and responsibilities should be assigned.
This is complicated by the fact that companies often hire third-party consultants to help with the WMS implementation, taking on work otherwise done by the company and/or the WMS vendor.
That said, a high-level organization chart of what a typical WMS project team looks like is provided below:
Typical WMS Project Organization Chart
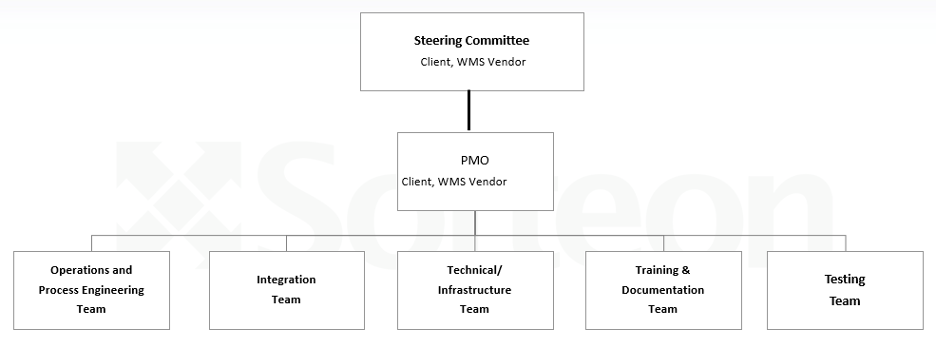
The specific roles of each of these functions is summarized below:
Steering Committee:
- Provides and Sets Overall Business Guidance
- Decides Critical Success Factors
- Approves Budget and Timeline
- Project Go-Live/No-Go Approval
- Responsible for Approving Capital, Timeline Changes and Resources
Project/Program Management:
- Overall Work Plan Management
- Facilitates Business Change Readiness
- Budget Management and Resource Allocation
- Risk Management and Issue Resolution
- Project Communication and Status Reports
- Manages Escalations
Operations and Process Engineering:
- Responsible for Operational Changes Due to ‘To Be’ Processes
- Implements Operational Change Control Processes
- Assists in Scheduling Project Roll-Out
- Validates the CRP (Conference Room Pilot)
- Implements New Processes (If Applicable)
Integration:
- Responsible for External/Internal System Interface Design Process
- Responsible for MHE Interfaces (If Applicable)
- Executes Interface Testing and Validation
- Develops Conversion Program Designs and Specs
- Tests and Validates Conversion Programs
- Supports System Conversion and Start-Up
Technical/Infrastructure:
- Infrastructure Design and Implementation
- Defines the Overall Product Design
- Software Configuration
- Software Design and Development
- Interface Design and Development
- Delivers the Product
Training and Documentation:
- Designs and Develops Training Materials
- Trains the Trainers
- Trains the End Users
Testing:
- Designs and Develops Test Plans
- Conducts Application Testing
- Conducts Integration Testing
- Leads User Validation Activities
- Responsible for Report Design Specifications
Make Sense of WMS, WCS, and WES.
Understand the differences and how they work together to optimize your operations.
How Long does it Take to Implement a WMS?
There is no easy answer to this question, as it depends on many factors. Those include: project/process complexity; amount of materials handling automation; and critically, the level of resources a company can bring to the WMS project.
A common problem is that individuals with less than full-time assignment to the implementation – for example, 50% – do not meet those planned time and effort allocations. That means the needed work is pushed out, jeopardizing either hitting the go-live date, or – worse – going live as scheduled but encountering many problems from a lack of proper preparation, testing, etc.
The internal resource allocation issue needs to be examined with brutal honestly before the project is officially kicked-off.
Softeon commonly implements even complex WMS solutions in 4-5 months, generally more rapidly than other providers.
Other Tips for a Successful WMS Implementation
Below are some tips for WMS implementation success:
- Identify the specific person who has the authority to make the final decision when questions/issues come up during testing and go-live.
- During the implementation period, keep a detailed log of all issues/questions and what decisions are made relative to those issues and why.
- It’s often cited that insufficient system testing and user training is the most common cause of implementation problems.
- Plan early for what kind of data (such as purchase orders/ASNs and order files) will be needed for system testing, with a plan for producing this data and providing it to the WMS vendor.
- Have a plan for providing sufficient physical product that will be needed for testing as well (pallets of goods for receiving and putaway, cartons or other handling for picking and replenishment, etc.) – this is a frequently overlooked requirement.
Delivering WMS Success Every Time
Only Softeon has a 100% track record of WMS deployment success – unmatched in the industry.
That history of successful deployments is a result of several factors, including a highly configurable solution that rarely requires modifications; an iterative project methodology that quickly identifies complete operational requirements; a set of tools, including a simulation capability for testing ERP and material handling systems well before go-live; highly experienced project leaders; and a unique “hyper-care” program after go-live that is focused on delivering time-to-value and rapid achievement of throughput goals.
Softeon is also the only major WMS provider to offer fixed-price WMS deployments.
With Softeon, your project will be on-time, on-budget – and on-results.