Casey’s General Store Case StUdy
Grocery and Retail
Terre Haute, IN
North America
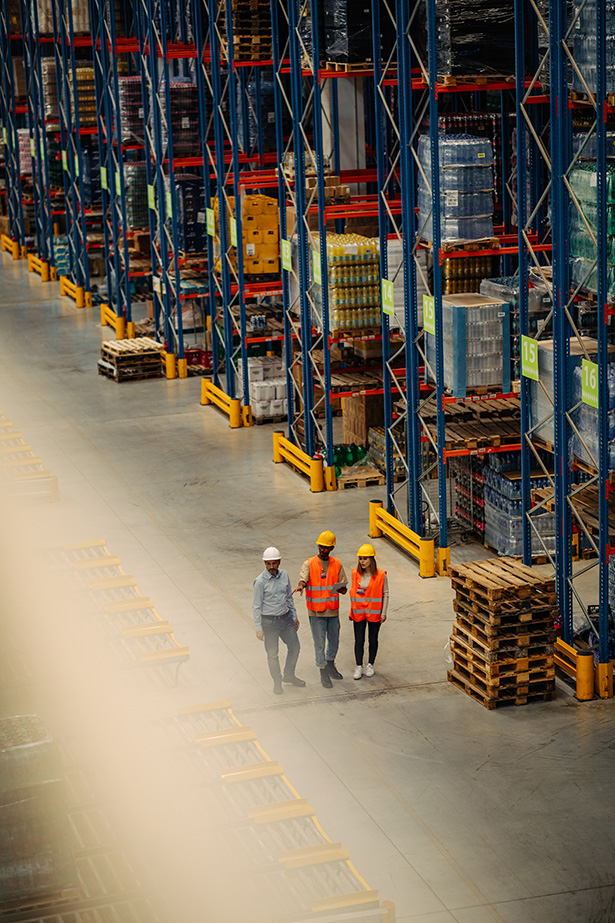
Overview
Casey’s started as a neighborhood country store that has continually transformed over the years in response to the community’s burgeoning patronage and their increasing needs. Today, Casey’s has grown into a community staple with 1,900+ stores. All of these stores were serviced weekly by a fleet of trucks from a single distribution center in Ankeny, Iowa until February, 2016, when Casey’s opened a second distribution center in Terre Haute, Indiana.
Business
Challenge
Casey’s was using a homegrown warehouse management system for many years. In 2014, a decision was made to replace it after it was clear that limitations in the system were hindering business growth. Maintaining and supporting the system required significant resources and time. Most importantly, the existing legacy system was not designed to support more than one distribution center.
The need to upgrade the warehouse management system, along with other systems, became critical when the decision was made to open a second distribution center. It was important that this new system be robust and flexible, rules-driven and easily integrated into the existing IT infrastructure. In addition to these features, the new system would need to provide corporate wide visibility to all data in real-time, and support automation and voice operations. Most importantly, Casey’s required the solution implementation to have a guaranteed cost and time frame for completion.
Softeon Solution
Casey’s selected Softeon’s Warehouse Management System and Plan-to-Fulfill solutions to fuel growth and improve operations. In Softeon, Casey’s knew they had the right technology partner – a partner that not only offered best-of-breed solutions but one that was committed to Casey’s success.
The Softeon WMS solution met all of Casey’s objectives on-time and on-budget. The first DC went live 5 months from the start of the project, and the newest DC was enabled in less than 2 months. Casey’s experienced immediate value in terms of increased productivity, reduction in inventory carrying costs and network-wide real-time visibility. Softeon WMS also provided improved tracking abilities, allowing Casey’s to track and comply with potential changes in The FSMA (Food Safety Modernization Act) by the FDA.